This is an example of why you always check your assembly tolerances as you’re putting an engine together. The image that follows is the cam sprocket from an Edelbrock 7814 set I purchased last week.
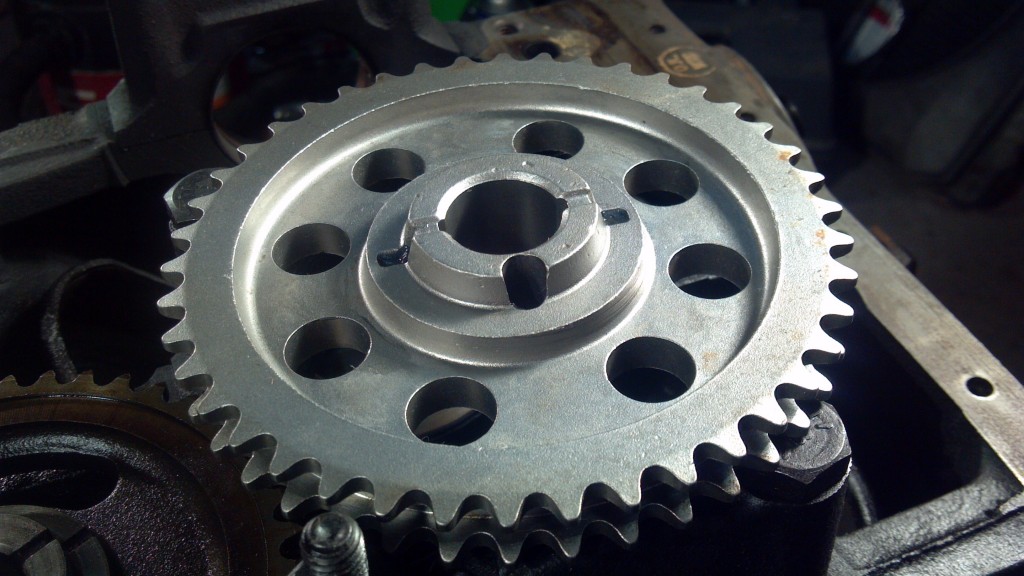
Can you spot what’s wrong already? If you can’t see it in the view above, click the link to the full resolution of the photo.
Ford uses a simple system to control camshaft end play. The sprocket face above bolts to the end of the front cam bearing journal, creating a gap between the second step on that sprocket and the journal face. Sandwiched in that gap is a hardened steel or cast iron camshaft retainer plate. The difference in thickness between the gap and the plate thickness ends up being the end play.
When putting together an engine, my normal procedure is to install the cam, bolt up the cam sprocket temporarily so that I can check end play while it’s easy to get to, and then remove the cam sprocket and proceed to the crank and the rest of the rotating assembly.
Since I always measure and remove anyway, I didn’t pay too much attention to the new cam sprocket when I was installing it last night, which gave me ZERO end play once installed. The cam would turn by hand, but I was probably less than a thousandth of an inch of luck from full bind. Of course, running the engine in this state probably would have lunched the build very quickly, which is why it’s best to measure everything as it goes together.
I was re-using the original cam with a new camshaft retainer plate, so my first thought was a machining error in the Ford plate. I swapped to the old Ford retainer plate and got the exact same result.
I’d have saved myself about ten minutes of head scratching if I’d looked at the sprocket first. If you look at the two protruding faces, neither is machined. They are both as-cast surfaces. You can see a bit of the hub of the original sprocket in the bottom left of the photo, for a comparison of what that finish should look like. Or, just take a quick peek below.
Simply put, someone at the factory making this part for Edelbrock just missed a step. At some point during manufacture of this piece, it should be chucked in a lathe, and those two surfaces turned to meet the end play tolerance. Someone just missed it. This surprised me, since it’s the only defective part I’ve ever personally gotten from Edelbrock.
Luckily, a phone call quick trip to Advance the this morning before work got me a part that was completed. I’d bought their only 7814 in the region, so I paid another $12 and swapped to an Edelbrock 7811, which is interchangeable with the 7814 other than a pair of extra keyways to advance and retard the cam timing. Problem solved, no hassle, and my one Edelbrock “oops” will go back to them.
Here’s the 7811 with the correct machining. You can see there are four lathed surfaces here that were missed on the first one.
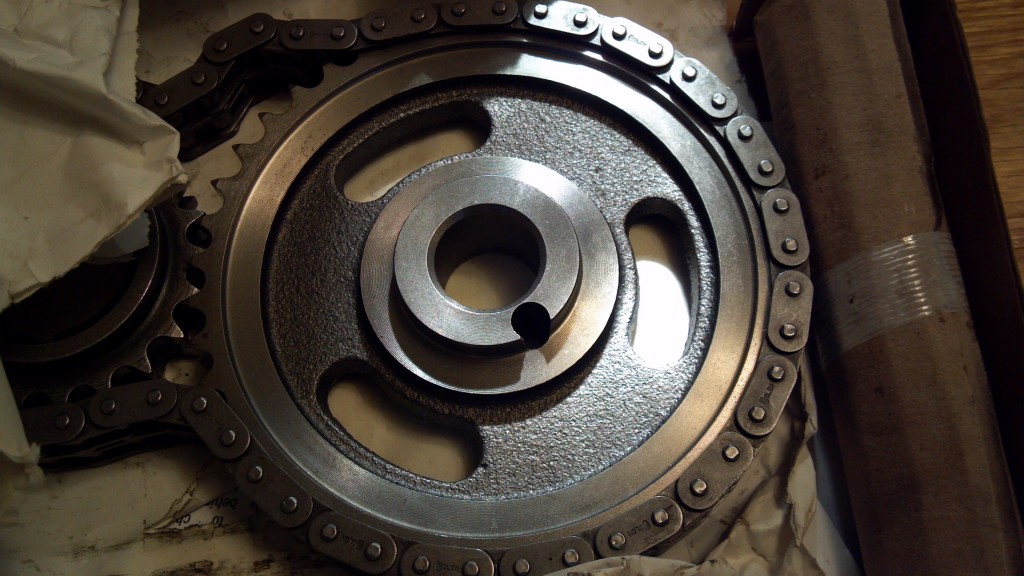
A Note on Measuring Camshaft End Play
I’ve noticed a very common and very critical omission in most of my shop manuals that turns up on forums fairly often. Off the top of my head, this tidbit is missing in two Ford factory shop manuals I own (1993 Mustang and 1991 Truck), as well as a smattering of Haynes and other manuals I have.
All of these references instruct you to install the cam, install the retainer plate, check the camshaft end play (the tolerance is 0.0055-0.009 for fuel injected 302’s), and then install the timing set.
If you follow these instructions as they appear in every manual out there, you will do a lot of head scratching, because you’ll see anywhere from 1/10 to 1/4 of an inch of camshaft end play. Don’t worry!
How to measure camshaft end play (the one and only way that actually works):
- Install camshaft
- Install retainer plate
- Install and torque cam sprocket
- Measure end play
- Remove sprocket so that you can install remainder of timing set
Without the sprocket installed, the only thing controlling your end play is the plug in the camshaft bore all the way in the back of the block. The sprocket must be installed in order to measure, but I have yet to find a manual that points that fact out, at least in my collection.
This little anecdote is personal experience, as I was one of the head scratchers the first time I ran into this.